Plastiform mise sur la production en environnement contrôlé
Publié le 11 sept. 2024, Modifié le 15 oct. 2024 - Écrit par Tiphaine Ruppert-Abbadi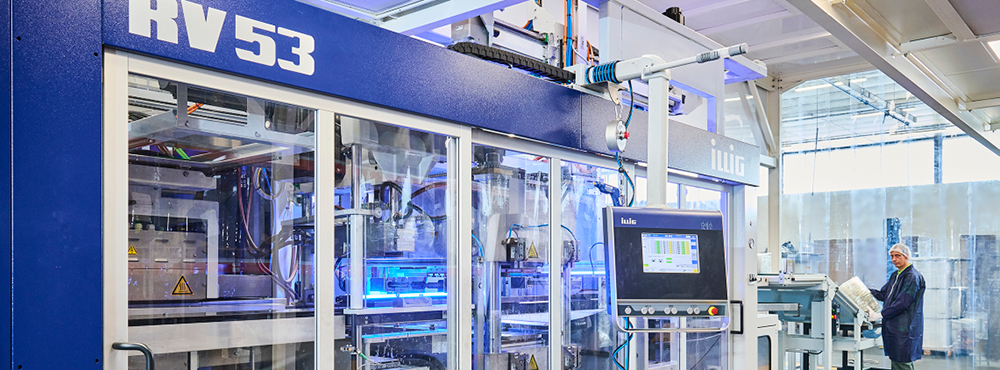
Produire en environnement contrôlé, c’est le défi que s’est lancé Plastiform, à Thise (25). En avril 2023, la société spécialisée dans le thermoformage sur-mesure a ainsi emménagé dans un nouveau bâtiment de 2 000 m², libéré à la suite du départ d’Antolin. Le nouveau site complète l’atelier historique, qui conserve la production sur machines à plaques et semi-automatiques, ainsi que l’usinage. Il est doté de 5 machines. Depuis juillet dernier, l’une d’elles est équipée pour produire dans des conditions de propreté extrêmement rigoureuses.
Cette RV53 D de chez Illig est installée dans une zone propre qui bénéficie d’un système de flux laminaires de type ISO 7. "Dans cet environnement contrôlé, délimité par des lames PVC, l’air en surpression est poussé vers le bas, puis vers l’extérieur de la machine et de la zone propre", explique Olivier Rodary, le directeur général. En outre, le nombre de personnes et les mouvements à l’intérieur du sas sont limités : 5 à 7 travaillent sur le site, mais 1 seule à la fois peut accéder à la machine. Le système d’empilage des pièces en sortie de ligne a été revu et celles-ci sont désormais récupérées par un robot servo-motorisé muni de ventouses. Les matières sont choisies en fonction de leur capacité à émettre le moins possible de particules. Elles ont le plus souvent elles-mêmes été produites en environnement contrôlé et parviennent sur le site avec un double emballage plastique. "Nous sommes assez peu nombreux à posséder ce type d’équipement, pour l’instant nous sommes en avance, mais c’est une demande qui augmente dans tous les secteurs. Les pièces sont de plus en plus précises et le niveau de qualité attendu de plus en plus exigeant, [avec une tolérance] de l’ordre de 100 à 200 µ pour les particules métalliques et de 200 à 400 µ pour celles plastique", détaille le chef d’entreprise. Des contraintes qui s’appliquent y compris aux conditionnements thermoformés tels qu’en propose Plastiform, notamment pour pouvoir répondre aux commandes du médical, mais aussi de l’électronique, de l’automobile, de l’aéronautique ou encore du luxe.
L’aménagement de cette unité de production propre a nécessité un investissement de 700 000 €, dont 200 000 € rien que pour le système de flux luminaire et l’extraction de chaleur. Une dépense intégrée à deux programmes d’investissement, respectivement de 4,5 M€ et de 2,2 M€, menés dans le cadre de l’appel à projets France 2030. "Le plan de relance visait plusieurs choses, dont les recherches autour de la plastronique et plus spécifiquement, chez nous, de la technologie IME. La création de la zone propre est aussi liée au développement de ce procédé innovant", précise encore Olivier Rodary.